This website uses cookies so that we can provide you with the best user experience possible. Cookie information is stored in your browser and performs functions such as recognising you when you return to our website and helping our team to understand which sections of the website you find most interesting and useful.
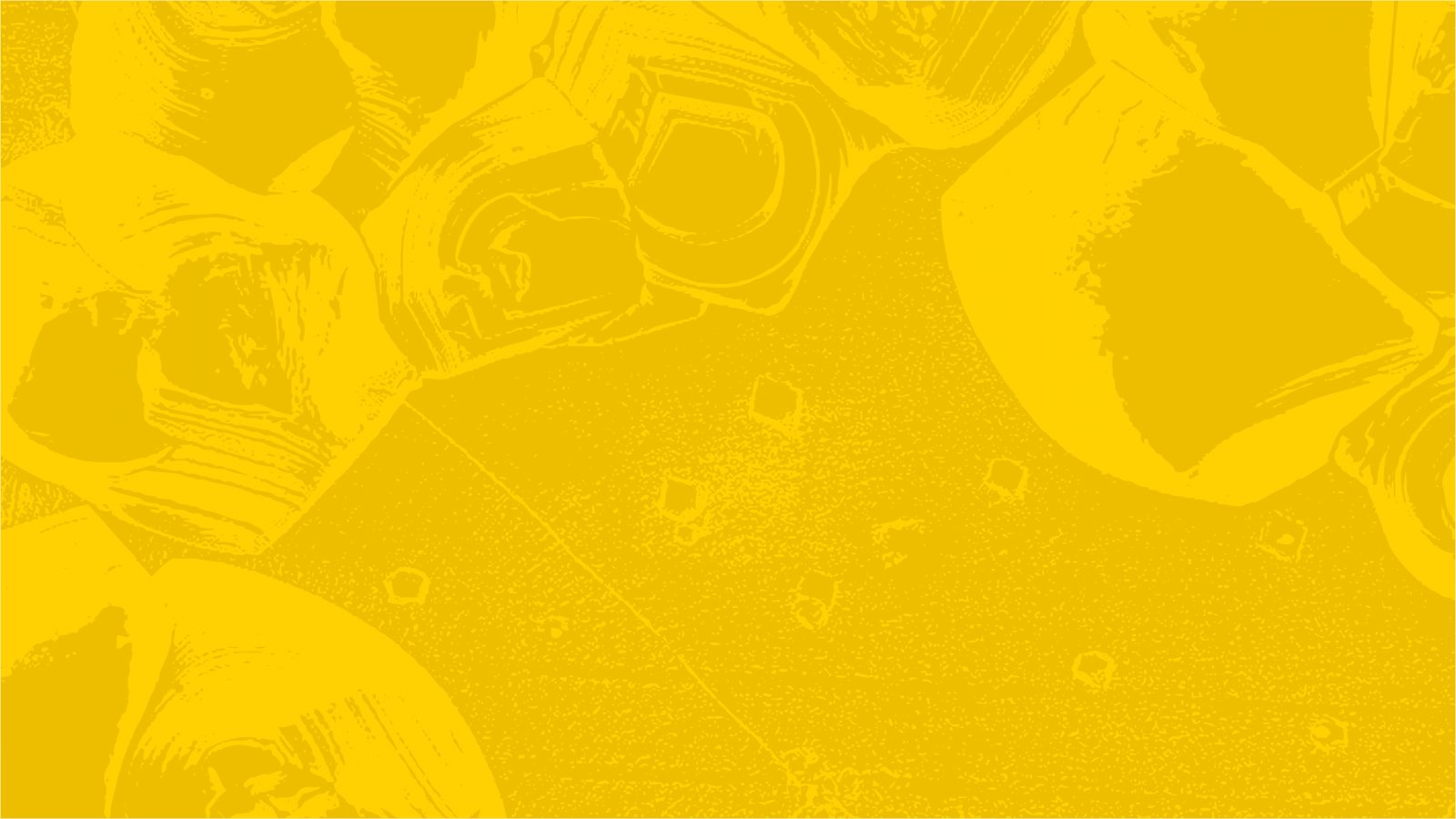
High-Temperature, High Pressure Degradation Environments
Technology Platform
About
The interaction of environment and structural component integrity is a significant area of concern for a large range of industries where high integrity is required. This includes civil nuclear (Advanced Gas-cooled Reactor (AGR), Pressurized Water Reactors (PWR) and Boiling Water Reactors (BWR)), nuclear propulsion, conventional power generation, aero engines, gas turbines, steam turbines, and the oil and gas processing industries.
There are a host of degradation mechanisms (carburisation, oxidation, corrosion, corrosion-fatigue, metal dusting, stress corrosion cracking, strain-assisted grain boundary oxidation, oxidation assisted creep-fatigue, hydrogen embrittlement, etc) which are unique to the environment in which components operate. Moreover, the role of hydrogen in assisting environmental cracking is still not clear, and the availability of a hydrogen charging facility is a useful aid to understanding material performance as well as the wider applications in the hydrogen economy (including steam methane reforming reactors, and hydrogen storage and distribution). In many cases the fundamental understanding of these degradation mechanisms is weak.
Royce has thus made a significant investment in the high-temperature, high-pressure (HTHP) facilities to improve the fundamental understanding of some of these mechanisms in the expectation that it will result in better solutions to these industrial challenges.
Platform Lead
Dr Fabio Scenini
Technology Platform Lead: High-Temperature, High-Pressure Degradation Environments
Dr Scenini holds an MEng in mechanical engineering from the Politecnico di Milano (Italy), an MSc in corrosion from UMIST and a PhD in environmentally assisted cracking from the University of Manchester. He is currently a Reader (Associate Professor) at the Materials Performance Centre at the University of Manchester. As an internationally recognised research scientist in materials performance and corrosion, he undertakes impactful research with real-world applications, of particular relevance to the Energy and Advanced Materials Performance research beacons. He currently leads the Materials Performance Centre theme “Environmental Effects on Reactor Plant Materials” within the Materials Performance Centre at the University of Manchester, and also the HTHP sub-theme within the Henry Royce Institute.
His current research interests are in material performance issues such as corrosion, stress corrosion cracking, fatigue and fracture, and hydrogen embrittlement particularly of the stainless steels and nickel base alloys employed in nuclear power plants and the aerospace industry. He has authored over 100 publications, covering journals and peer-reviewed conference proceedings.
Equipment
We have a suite of autoclaves and recirculating loops capable of testing materials in ultra-high purity, HTHP water environments relevant to light-water reactor nuclear power plants. Systems are capable of operating in hydrogenated, oxygenated or mixed water environments with lithiated, borated or potassiated water chemistries achievable. Water chemistries can be controlled and monitored through the use of pH, conductivity, and dissolved oxygen and hydrogen sensors.
Two environmentally assisted cracking (EAC) autoclaves and recirculating loops, coupled with 100kN tensile machines with the capability for ultra-slow rate strain, constant load, and low-cycle fatigue testing. Crack growth monitoring can be carried out through instrumentation with a Direct Current Potential Drop system. The volume of each 316L stainless steel autoclave is 12.5 litres, allowing testing of up to 3 x 1T Compact Tension samples either in oxygenated or hydrogenated PWR water at temperatures of up to 360°C and 200 bar pressure.
Four Slow Strain Rate Testing (SSRT) autoclaves and recirculating loops, capable of constant load, ultra-slow strain rate testing and low cycle fatigue testing at up to 360°C and 200 bar in oxygenated or hydrogenated PWR water. Tested samples can be either 0.5T compact tension specimens or dog-bone type tensile specimens at loads of up to 50kN. Crack growth monitoring can be carried out through instrumentation with a direct current potential drop system. Three of the systems are manufactured from 316L stainless steel, and one is from Hastelloy C-276 allowing caustic environments to be tested.
Two sapphire-windowed imaging autoclaves and recirculating loops with the capability for uni-axial or bi-axial four-point bend loading of samples at up to 10kN. The sapphire windows are positioned to allow for optical viewing of the portion of the sample that is under tensile loading. Vessels and loops are manufactured from 316L stainless steel with testing in oxygenated or hydrogenated PWR water at temperatures of up to 250°C and 350°C respectively.
Three autoclaves and recirculating loops for oxidation and electrochemical studies at up to 350°C and 200 bar in hydrogenated, oxygenated, or doped PWR or BWR water chemistry. Three systems are manufactured from 316L, and one system is manufactured from titanium for oxidation characterisation studies.
One galling autoclave and recirculating loop for wear or galling testing of samples in accordance with ASTM G196 in oxygenated or hydrogenated PWR water at temperatures of up to 350°C. The system is manufactured from Hastelloy C-276.
One sapphire-windowed autoclave and very high flow loop capable of simulating corrosion related deposit (CRUD) formation or sub-nucleated boiling on a heated rod within the autoclave. Hydrogenated and oxygenated PWR water chemistries at up to 340°C can be achieved, and the system is manufactured from 316L stainless steel.
One static autoclave with a volume of 0.9L manufactured from Alloy 625 and rated at up to 360°C for testing in aggressive water chemistries.
Hydrogen autoclave capable of hydrogen charging in pure hydrogen environment at temperatures up to 300°C and pressures up to 300 bar whilst conducting test at slow rate strain, constant load or low-cycle fatigue testing. Crack growth monitoring can be carried out through instrumentation with a direct current potential drop system. The large 3L volume of the autoclave also allows the exposure of samples for post-charging, ex-situ testing.