This website uses cookies so that we can provide you with the best user experience possible. Cookie information is stored in your browser and performs functions such as recognising you when you return to our website and helping our team to understand which sections of the website you find most interesting and useful.

Partner
The University of Manchester
Introduction
The University of Manchester is the largest single-site university in the UK, with the biggest student community hailing from 160 countries. A member of the Russel group with 25 Nobel Prize winners who have worked or studied here. With a turnover of £987 million in 2015–16, of which £273 million for research, the University is carrying out the biggest investment in facilities undertaken by any UK university, with £750 million spent so far and a further £1 billion to follow by 2022.


Royce Facilities
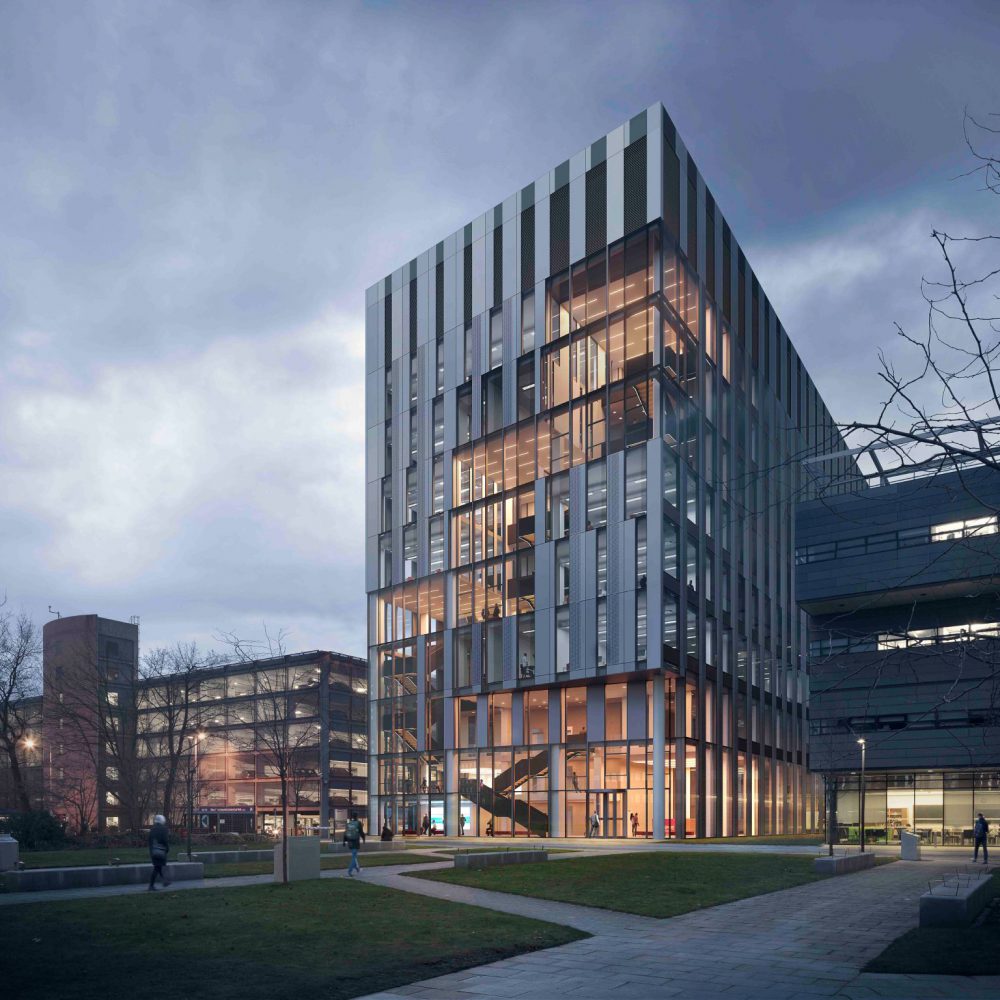
New Royce Building
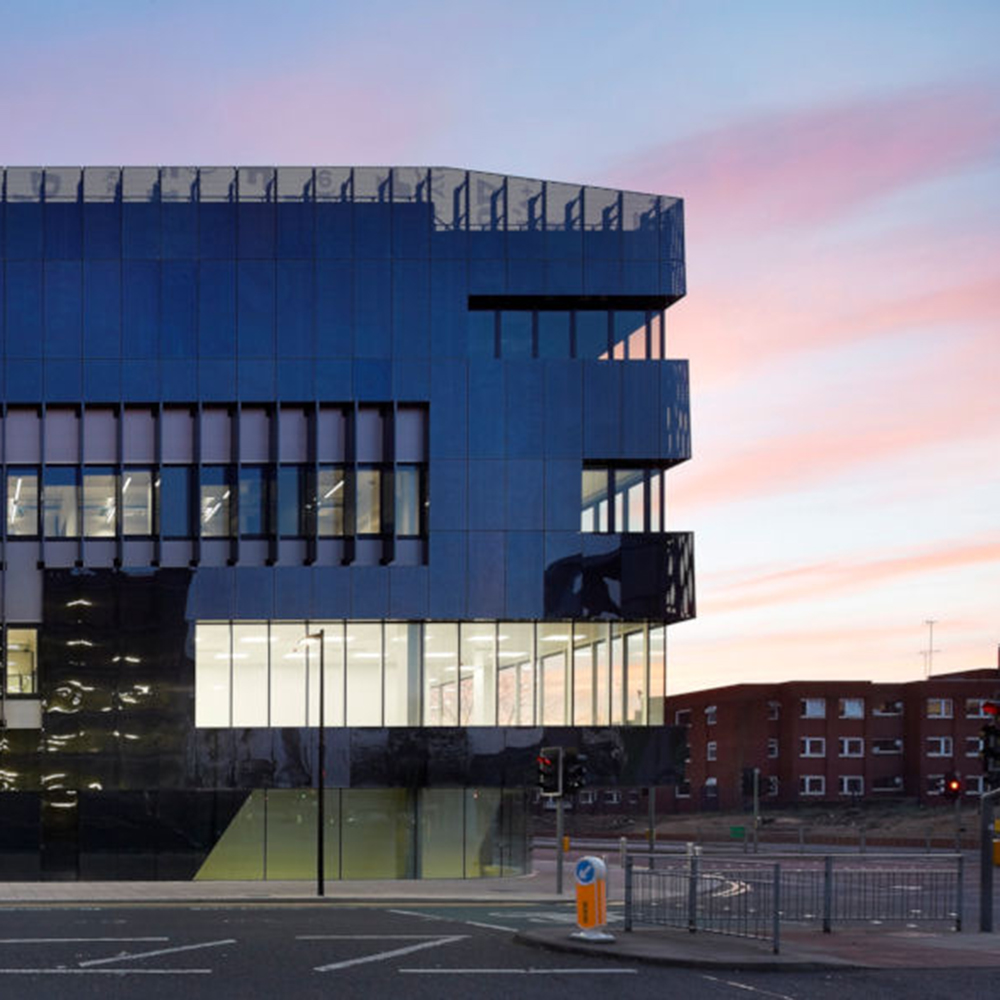
The NGI houses academics and industry partners, working side by side on the applications of the future


The University houses more than £200m of Royce facilities and equipment. Central to the University of Manchester’s materials science activity is the Royce Hub Building, which was completed in 2020. The £105m, nine-story building at the heart of the University’s Engineering Campus is the home to world-leading materials scientists, £45m worth of equipment and collaborative space for industrial and academic engagement. The building design is intended to allow ‘Science on Show’ – areas of the building visible to engage people outside – while also providing closed, confidential spaces for commercially sensitive work. In addition to the new Hub building, state-of-the-art facilities across the University are also part of Royce. The cleanrooms at the £61m National Graphene Institute (NGI) – the world’s largest single use graphene cleanrooms – are used by Royce 2D Materials researchers. Scientists from the Nuclear Materials research area work in the Dalton Cumbrian Facility (DCF), a specialist radiation science and nuclear engineering decommissioning site. The high-quality microscopy facility at the Henry Moseley Centre in the Photon Science Institute is also be part of the University’s Royce capability, and the new 350m Manchester Engineering Campus Development (MECD) houses further microscopy equipment. The range of facilities and equipment at the University shows the strategic importance of Royce and the interdisciplinary focus of its research activities.

Core Research Areas
Two-dimensional materials are one-atom thick materials capable of being combined in nano-stacks to deliver unique functionality. By far the best known is graphene, but there is a large and growing famly of 2D materials that promise to revolutionise the materials world. 22D materials were pioneered in the UK, following the isolation of graphene at The University of Manchester in 2004, and, since then, they have become the subjects of a massive international research effort, due to their potential to influence a number of areas such as membranes for filtration and coatings, energy storage and functional composites.
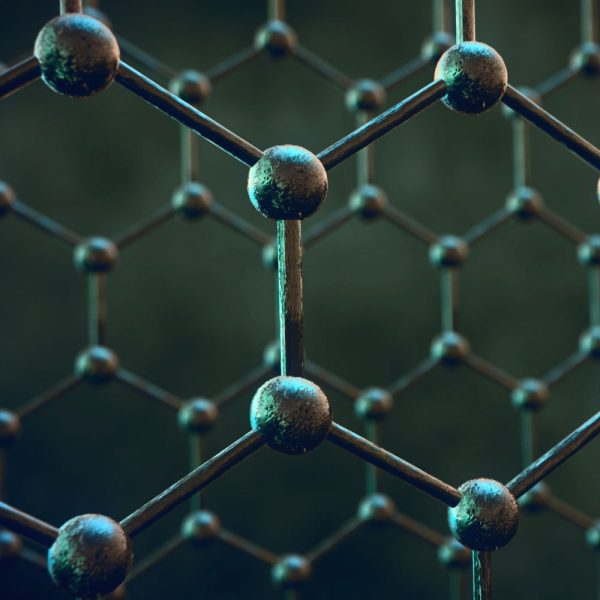

Novel medical approaches to improve human health and well-being are essential for maintaining the UK’s internationally leading position in medical technology. A new generation of “smart” biomaterials is required. The Biomedical Materials is a key theme within Royce and the intention is to accelerate the discovery, manufacture and translation of biomaterials through a platform of state-of-the-art equipment. The two identified grand challenges of advanced biomaterials research are restoring biological function with minimal invasiveness (e.g. regenerative medicine, novel prosthetics and implants) and developing new therapies that reduce patient risk, improve efficacy, and lower cost (e.g. nanomedicine theranostics and personalised medicine). This theme will deliver: Direct patient benefit by replacement of damaged tissues via regenerating worn out or torn cartilage using only biodegradable biomaterials; 3D in vitro tissues for improved pharmaceutical testing which could reduce reliance on antibiotics; Significantly reduce the need for animal testing; Reduce the overall cost of production of medical devices. Through improving the manufacturing process of currently used biomaterials and the creation of more devices that could be surgically inserted using minimally invasive techniques would have a significant global impact in terms of healthcare provision.
To deliver science and innovation in advanced materials for nuclear applications driving impact and economic benefit for the UK. Nuclear activity can be split into two areas: Nuclear fuels and waste streams in the nuclear fuel cycle; Structural materials for fission and fusion energy. We could see: Fuel production and performance including accident tolerant fuel; Energy & materials co-production; Waste conditioning & disposal; Self-healing coatings; Novel nuclear structural materials; Mechanical properties and irradiation effects in engineered alloys. The Nuclear research area will establish Royce capability for scientists and industry to prepare, test and analyse radioactive materials for fission and fusion applications. It will enable substantial programmes of work on authentic irradiated nuclear materials and support The Industrial Strategy. Our researchers will deliver innovation in materials, materials performance data and understanding to reduce costs and increase productivity in current and future nuclear programmes And we will exploit advanced materials with confidence and the data necessary to underpin safety.
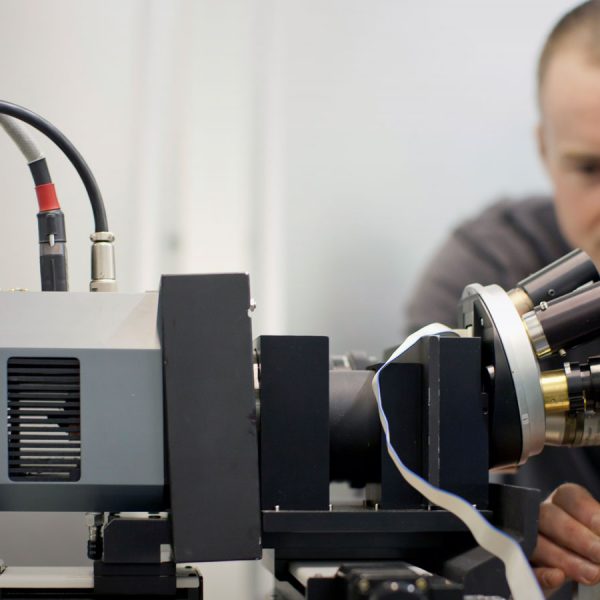
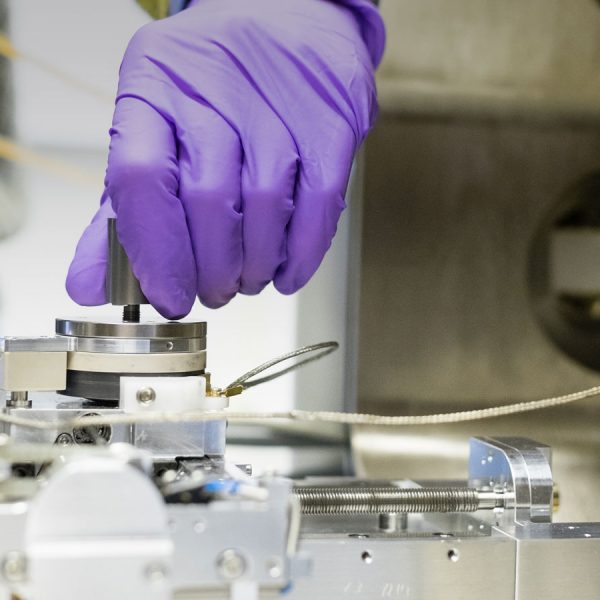
For industrial applications demanding environments are present everywhere and corrosion is all around us; whether that is in energy production, the marine sector or the aerospace and automotive sector. Corrosion can also be important in the medical sector as implants need to function in very extreme and unusual conditions. It is important to have safe materials for biomedical components, as well as for these heavy engineering components for example plant, infrastructure and transport. We will design, make, characterise and test new material systems for demanding environments, supporting energy, transport and other sectors. This theme has a large research capability on nuclear fuel cladding and high-pressure, high-temperature research, including a large autoclave testing facility. The overriding aim is to develop materials solutions and systems that will enable a ‘step-change’ in component development for applications in aggressive environments. A crucial aspect of developing these new material systems is to fully understand the relationship between the manufacturing parameters and performance of the material; a cradle-to-grave approach. Imagine the benefit of turbine blade coatings which were self-healing, or the environmental impact of erosion-resistant coated piping with sensor capability, the economic and human impact of nuclear fuel assemblies could withstand accident scenarios for hours instead of minutes. Through the Royce collaboration these are all possibilities.