This website uses cookies so that we can provide you with the best user experience possible. Cookie information is stored in your browser and performs functions such as recognising you when you return to our website and helping our team to understand which sections of the website you find most interesting and useful.
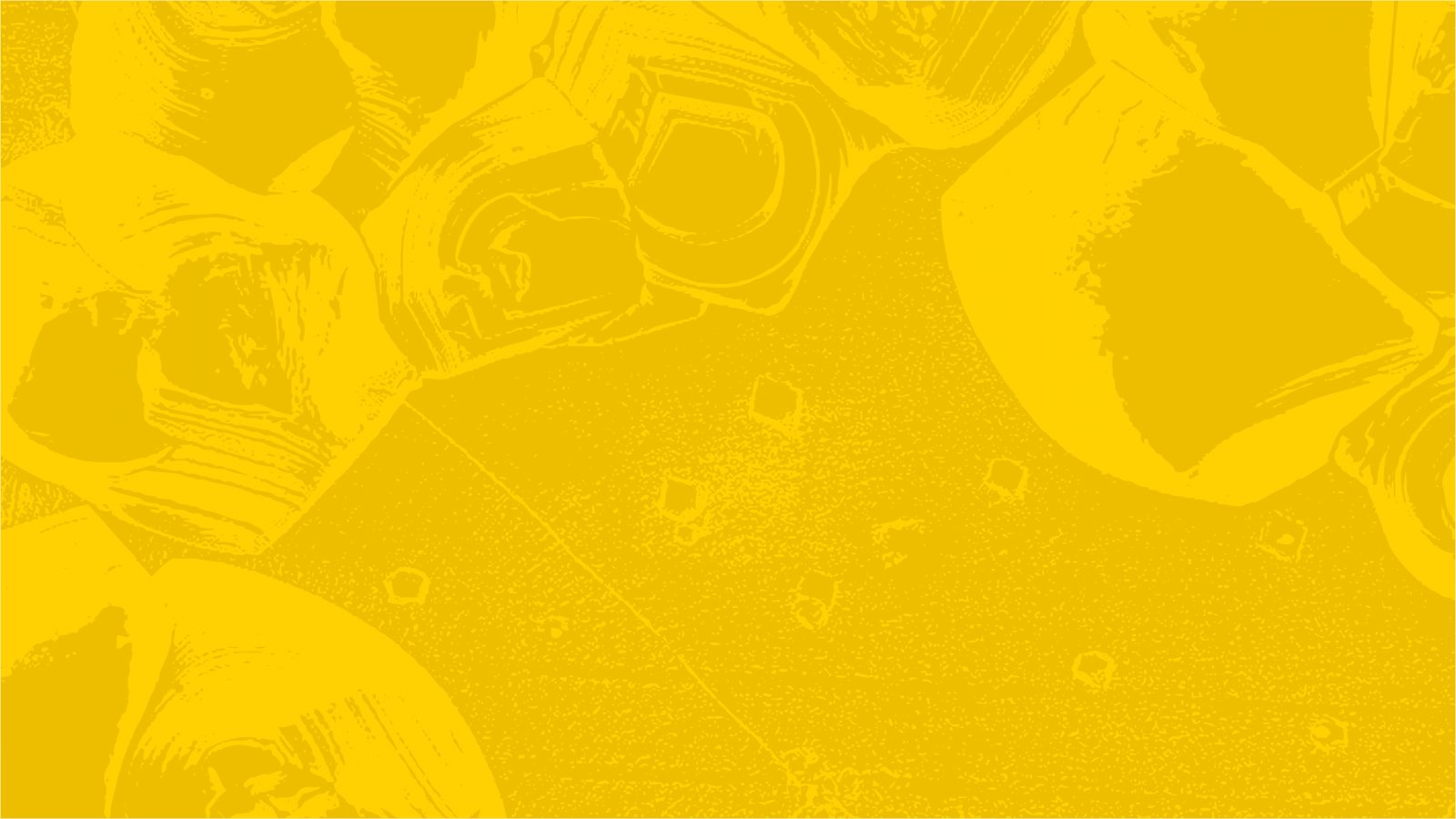
Developing A Novel Composite Cure Monitoring Solution Using Customised Graphene Inks
Case Study
Overview
DZP Technologies and the University of Sheffield Advanced Manufacturing Research Centre (AMRC) collaborated towards development of a novel composite cure monitoring solution using customised conductive inks.
The project experimented with graphene ink formulations and printing methods to create advanced sensors for composite materials, replacing traditional sensors. Initial tests showed challenges with conventional di- electric based cure monitoring, but promising results with strain-based monitoring using graphene sensors.
The project also had to resolve challenges with compatibility with prepreg resin materials and functional conductive inks. Improved consistency was achieved using the high- precision screen printer at the Maxwell Centre at the University of Cambridge.
Future work will focus on improving printing techniques and the knowledge gained will be used to develop artificial intelligence for better sensor data analysis, helping improve sensor functionality for tasks such as structural health and cure monitoring.
About the Project
DZP Technologies collaborated with AMRC towards development of a novel composite cure monitoring solution by exploring the use of customised conductive graphene inks as sensors. Polymer composites are widely applied across various sectors due to their superior mechanical performance. Monitoring the degree of cure is vital to optimise properties during composite manufacture. However, traditional sensors are fragile, expensive, and inflexible. This project aimed at developing a cure monitoring solution using DZP’s conductive inks with varying graphene formulations for customised electrical and thermal responses.
Using its manufacturing expertise, the AMRC composites team conducted cure monitoring, initially via Dielectric Analysis (DEA), and subsequently via strain-based graphene sensors.
Initial results indicated that the graphene-based dielectric sensors were less suitable and could not reach the accuracy of traditional metallic sensors. The focus of the work, therefore, pivoted to novel strain-based monitoring of the progression of cure. DZP down-selected several high potential graphene inks for this application. Thermal cycling and curing trials were completed using four graphene ink formulations and two substrates – dry glass fibre and cured glass fibre reinforced polymer (GFRP); with material manufacture reflecting two common composite manufacture processes – resin infusion and prepreg layup. Throughout the research, several challenges were identified, such as compatibility with prepreg materials and printing process controls for substrates and inks not commonly applied on the printer. Theoretically, printing directly onto GFRP prepreg provides an elegant solution for embedding sensors into both GFRP and carbon fibre-reinforced plastic structures.
However, this approach entails many challenges due to chemical side reactions which can render the materials unusable. This challenge was overcome through extensive investigation of different ink formulations – enabling direct printing of sensors onto prepreg to improve cure monitoring for future work. A further challenge to advancing the technology comes through the printing process control for sensor manufacture, which must ensure consistent and reliable sensor performance, even when challenging and variable printing substrates and inks are used. The printing consistency was improved using the high- precision screen printer at the Maxwell Centre, to understand and develop techniques for higher quality sensor manufacture. The printer will potentially be used for further development of the inks for application including, but not limited to, composite structures. The research discovered that the inks were responsive to factors such as temperatures and strain inputs, enabling them to act as multi-functional sensors. For instance, one of the inks was highly sensitive to the strain induced during resin flow across the sensor. A second ink formulation was indicative of temperature changes, whilst others showed complex responses consisting of multiple inputs.
These results provide DZP with direction for further ink development and sensor manufacture, opening the door for tailored ink formulations for specific responses. The knowledge developed in this research will be further exploited in an Innovate UK-funded project involving DZP, AMRC and other partners. It will develop artificial intelligence capabilities for improving monitoring of composite components during both manufacturing and operation.
The Royce Industrial Collaboration Funding allowed us to test an innovative application of our graphene sensors in composite manufacture. In collaboration with the AMRC at the University of Sheffield, we not only proved the feasibility of this interesting technology, but also gained significant experience, understanding, and knowledge of composite materials manufacture. We are now able to expand our presence in new markets and we are excited about business growth opportunities created as a result of this Royce funded project.
Zlatka Stoeva
Managing Director, DZP Technologies Ltd
Collaborators
The work was completed with lead organisation DZP Technologies Ltd, working with partners at University of Sheffield Advanced Manufacturing Research Centre.
The work was enabled due to a grant from the Henry Royce Institute’s Industrial Collaboration Programme, utilising Royce facilities at the Maxwell Centre, University of Cambridge.