This website uses cookies so that we can provide you with the best user experience possible. Cookie information is stored in your browser and performs functions such as recognising you when you return to our website and helping our team to understand which sections of the website you find most interesting and useful.
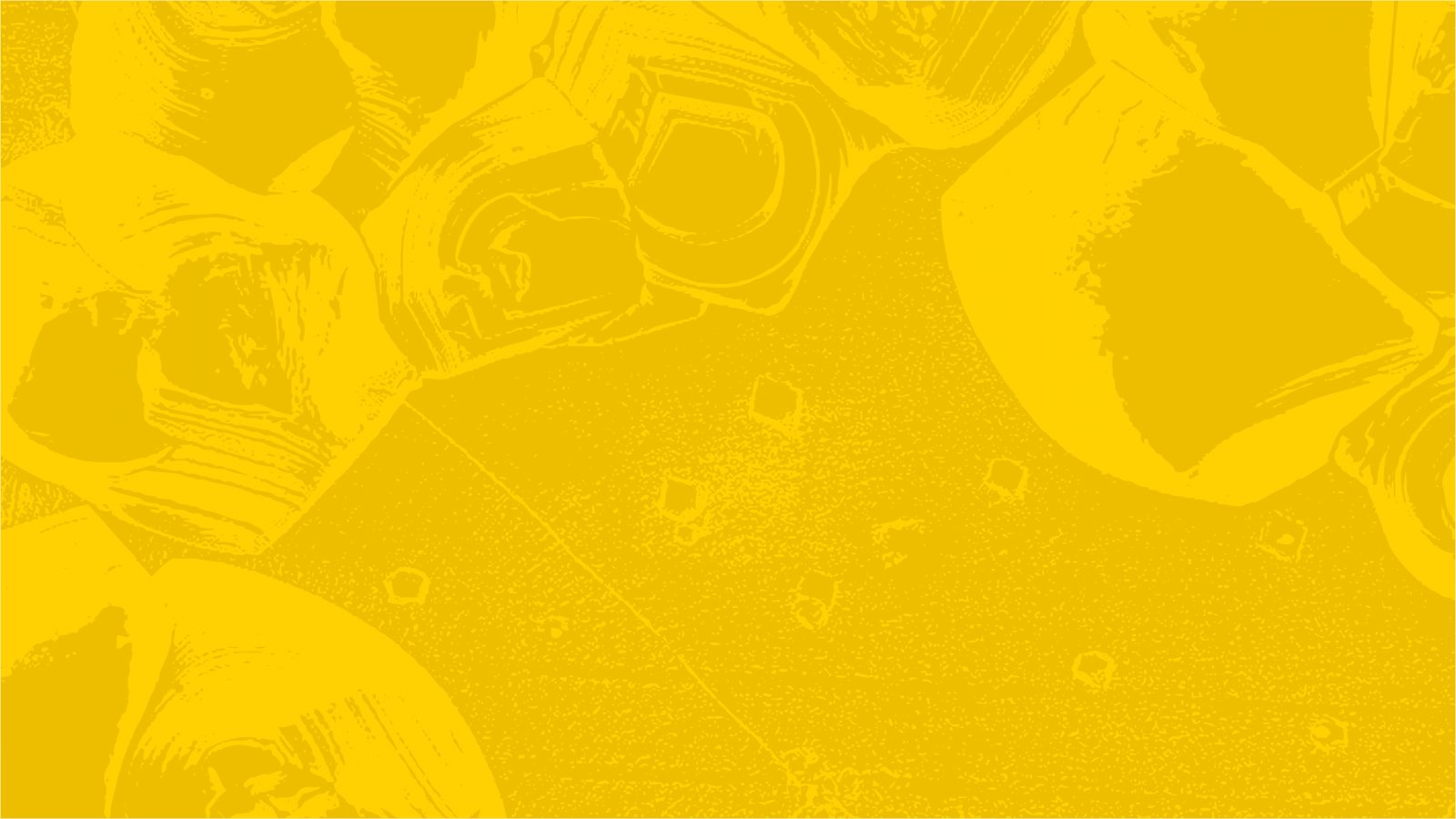
Hydrogen Embrittlement Testing Methodology Optimisation for Qualification of Aerospace Alloys (HOPTIMAL)
Case Study
Overview
Testing materials in relevant service conditions in contact with hydrogen is fundamental to certify materials for the hydrogen economy. The HOPTIMAL project aimed to compare electrochemical and thermal charging techniques in their effect on hydrogen embrittlement of austenitic stainless steel.
About the Project
Background
Qualifying alloy compatibility to hydrogen embrittlement in the laboratory environment is almost always performed in accelerated conditions, as testing in service conditions would lead to unreasonable testing times. For the two most employed hydrogen charging methods, cathodic charging, and gaseous hydrogen, this means increasing current density and pressure respectively. The type and parameters of hydrogen charging method, and when it is applied might bring different results, even for the same specimen. To produce reliable testing standards, the relationship between results obtained with different testing parameters and measured mechanical properties must be identified.
Project details and results
The HOPTIMAL project, a collaboration between Cranfield University, Darvick, Rolls-Royce and Reaction Engines, aimed at evaluating and comparing, for 316L steel, the effect of electrochemical and thermal charging on the hydrogen uptake and hydrogen embrittlement from room to low temperatures of austenitic stainless steel.
The project was subdivided into three tasks:
(1) development of electrochemical charging and discharging technique,
(2) design and build of tensile testing rig with in-situ electrochemical charging capability,
(3) Hydrogen quantification and embrittlement testing.
In Task 1, the electrochemical setup for both charging and discharging was developed at Cranfield University. The two techniques were developed in parallel as the amount of hydrogen charged had to be measured to assess the validity of the charging technique. The development in this task led to selecting deaerated Sodium Chloride and Thiourea as charging electrolyte and aerated Sodium Hydroxide in discharging. Several sample geometries were charged, from simple flat samples in preliminary tests, to cylinders and tensile specimens. Both charging and discharging techniques proved relatively reliable, although more work is required to prove their accuracy and repeatability.
In Task 2, the build was successfully built at Darvick, including a Platinum anode and a temperature-controlled recirculating bath (6l) system for the electrolyte. The task involved design, ordering of components, assembly, and validation. The rig was proven to perform reliably with minor pH changes over the time of charging (at conditions developed at Cranfield in Task 1). The rig is now accessible to use.
In Task 3, Darvick used their electrochemical rig to charge tensile samples both ex- (for up to 22h) and in-situ during the SSRT mechanical test (5·10-5s-1), using 5mA/cm2 current density. The results of the tests showed no significant difference at the tested conditions. More work is planned to assess the reasons behind this behaviour (e.g. higher current density, longer pre-charging time, etc.).
Low temperature tests were planned, also on pre-charged samples, at Cranfield University. Although the baseline tests with no pre-charge was successfully obtained showing expected results for 316L, no results from charged specimens could be obtained due to a technical fault in the equipment. These tests will be preformed post project completion.
Royce support
The Henry Royce Institute supported the project through funding the Cranfield mechanical testing capabilities used in Task 3, namely: High Cycle Corrosion Fatigue Rig for strain life testing and Advanced Potential Difference Corrosion Fatigue Rig for SSRT tests.
Future impact
The project significantly increased the knowledge on best practice to perform hydrogen charging for embrittlement testing. Results from this project will influence future hydrogen embrittlement testing standards and research direction worldwide. Several projects have already started or are being planned based on the learnings of the HOPTIMAL project, including hydrogen permeation in aluminium coated alloys for storage applications and electrochemical/thermal hydrogen comparison using a permeation apparatus.
The project has significantly improved our knowledge of best practice in testing for hydrogen embrittlement. Based on the results of this project, several activities have been planned or are already undergoing, including embrittlement of different materials and testing of hydrogen permeation barrier coatings. Although more work is required in this area, thanks to the Henry Royce Institute, this funding allowed a first step in the right direction.
Francesco Fanicchia
Senior Lecturer, Cranfield University
Collaborators
The work was completed with lead organisation Cranfield University, working in collaboration with Darvick Ltd, Rolls-Royce PLC and Reaction Engines.
The work was enabled due to a grant from the Henry Royce Institute’s Industrial Collaboration Programme.