Description
The Type H-HP D25 is our hybrid FAST/SPS furnace. It provides similar functionality to our small furnace, but the addition of an inductive heating system enables significant reduction of radial temperature gradients in larger-scale and/or insufficiently conductive samples. This ensures uniform density, microstructure, and properties across these samples, i.e. equipped with a radial, inductive heating system to prevent radial temperature gradients with large-sized components or to facilitate the inductive heating of materials that are otherwise inadequately conductive at room temperature.
Uses / Applications
FAST/SPS processing can consolidate a wide-range of metallic, ceramic, and functional materials. In general, the ability to utilise lower processing temperatures and/or shorter processing times allows the production of unique properties compared to conventional powder metallurgy sintering techniques, which make FAST/SPS attractive across a vast range of uses and applications.
Examples include:
– Sintered nanomaterial without significant grain growth
– Functionally graded materials
– Multi-material composite materials
– Innovative carbide metals
– Metal alloys (Ti, Ni, Al, Cu, Fe, W, V, etc)
– Intermetallic compounds
– Structural and functional ceramics
– Diffusion bonded materials
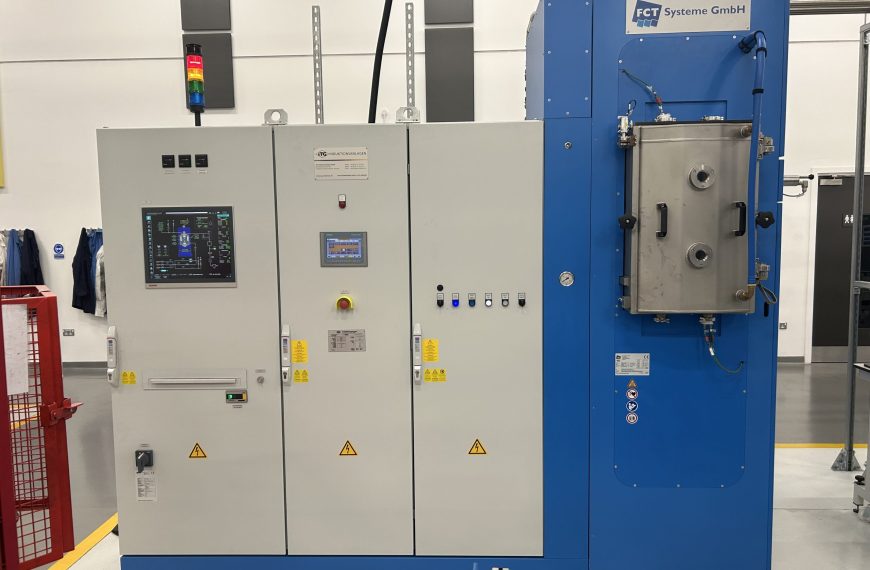
Specification
- Component size from 20 mm diameter to 100 mm diameter
- Maximum working temperature of 2200°C, with temperature measurement and control via axial/radial pyrometers and/or flexible thermocouples
- Heating rates of up to 500 K/min (depending on tool size and material)
- Fully programmable and customisable sintering cycles
- Comprehensive software for data recording and evaluation of all sintering parameters
- Vacuum level of 0.05 mbar or furnace atmosphere of Ar / N2
- Servo-hydraulic force control up to 250 kN, and measurement of displacement and densification rate
- Powerful induction heating coil for FAST Hybrid technology, allowing heating via FAST, Induction, or Hybrid (FAST + Induction) modes
- Maximum combined power of 140 kW.